Cross Contamination
Cross Contamination – noun – “inadvertent transfer of bacteria or other contaminants from one surface, substance, etc., to another especially because of unsanitary handling procedures. – (Mariam Webster, 2021). Cross contamination is not a new concept in the clinical and food lab industries; many facilities have significant design aspects as well as SOPs to deliver the least amount of contaminants into the lab setting. For cannabis labs, however, often the exponential growth leads to a circumstance where the lab simply isn’t large enough for the number of samples processed and number of analytical instruments and personnel needed to process them. Cross contamination for cannabis labs can mean delayed results, heightened occurrences of false positives, and ultimately lost customers – why would you pay for analysis of your clean product in a dirty facility? The following steps can save you the headaches associated with cross contamination:
Wash (and dry) your hands properly
Flash back to early pandemic times when the Tik Tok “Ghen Co Vy” hand washing song was the hotness – we had little to no idea that the disease would be fueled mostly by aerosol transmission, but the premise is the same, good hand hygiene is good to reduce cross contamination. Hands are often the source of bacteria, both resident (here for the long haul; attached to your hands) and transient (easy to remove; just passing through), as they come into contact with surfaces from the bathroom to the pipettor daily (Robinson et al, 2016). Glove use coupled with adequate hand washing are good practices to reduce cross contamination from personnel to a product sample. Additionally, the type of hand drying technique can reduce the microbial load on the bathroom floors and, subsequently tracked into the lab. A 2013 study demonstrated almost double the contamination from air blade technology versus using a paper towel to dry your hands (Margas et al, 2013).
Design Your Lab for Separation
Microbes are migratory. In fact, E. coli can travel at speeds up to 15 body lengths per second. Compared to the fastest Olympians running the 4X100m relay, with an average speed of 35 feet per second or 6 body lengths, this bacterium is a gold medal winner, but we don’t want that in the lab setting (Milo and Phillips, 2021). New lab design keeps this idea of bacterial travel in mind, but for those labs without a new build, steps can be made to prevent contamination:
- Try to keep traffic flow moving in one direction. Retracing steps can lead to contamination of a previous work station
- Use separate equipment (e.g. cabinets, pipettes) for each process/step
- Separate pre- and post-pcr areas
- Physical separation – use different rooms, add walls, partitions, etc.
Establish, Train and Adhere to SOPs
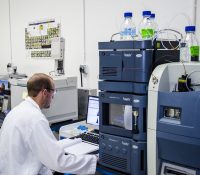
High turnover for personnel in labs causes myriad issues. It doesn’t take long for a lab that is buttoned up with cohesive workflows to become a willy-nilly hodgepodge of poor lab practices. A lack of codified Standard Operating Procedures (SOPs) can lead to a lab rife with contaminants and no clear way to troubleshoot the issue. Labs should design strict SOPs that include everything from hand hygiene to test procedures and sanitation. Written SOPs, according to the WHO, should be available at all work stations in their most recent version in order to reduce biased results from testing (WHO, 2009). These SOPs should be relayed to each new employee and training on updated SOPs should be conducted on an ongoing basis. According to Sutton, 2010, laboratory SOPs can be broken down into the following categories:
- Quality requirements
- Media
- Cultures
- Equipment
- Training
- Sample handling
- Lab operations
- Testing methodology
- Data handling/reporting/archiving
- Investigations
Establish Controls and Monitor Results
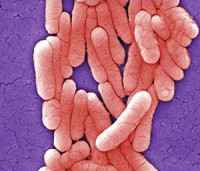
It may be difficult for labs to keep tabs on positivity and fail rates, but these are important aspects of a QC regimen. For microbiological analysis, labs should use an internal positive control to validate that 1) the method is working properly and 2) positives are a result of target analytes found in the target matrix, not an internal lab contamination strain. Positive controls can be an organism of choice, such as Salmonella Tranoroa, and can be tagged with a marker, such as Green Fluorescent Protein in order to differentiate the control strain. These controls will allow a lab tech to discriminate between a naturally contaminated specimen vs. a positive as a result of cross-contamination.
Labs should, in addition to having good QC practices, keep track of fail rates and positivity rates. This can be done as total lab results by analysis, but also can be broken down into customers. For instance, a lab fail rate for pesticides averages 4% for dried flower samples. If, during a given period of review, this rate jumps past 6% or falls below 2%, their may be an issue with instrumentation, personnel or the product itself. Once contamination is ruled out, labs can then present evidence of spikes in fail rates to growers who can then remediate in their own facilities. These efforts in concert will inherently drive down fail rates, increase lab capacity and efficiency, and result in cost savings for all parties associated.
Continuous Improvement is the Key
Cannabis testing labs are, compared to their food and clinical counterparts, relatively new. The lack of consistent state and federal regulation coupled with unfathomable growth each year, means many labs have been in the “build the plane as you fly” mode. As the lab environment matures, simple QC, SOP and hygiene changes can make an incremental differences and drive improvements for labs as well as growers and manufacturers they support. Lab management can, and should, take steps to reduce cross contamination, increase efficiency and lower costs; The first step is always the hardest, but continuous improvement cannot begin until it has been taken.
References
Margas, E, Maguire, E, Berland, C. R, Welander, F, & Holah, J. T. (2013). Assessment of the environmental microbiological cross contamination following hand drying with paper hand towels or an air blade dryer. Journal of Applied Microbiology, 115(2), 572-582.
Mariam Webster (2021. Cross contamination. Retrieved from https://www.merriam-webster.com/dictionary/cross%20contamination
Milo, M., and Phillips, R. (2021). How fast do cells move? Cell biology by the numbers. Retrieved from http://book.bionumbers.org/how-fast-do-cells-move/
Robinson, Andrew L, Lee, Hyun Jung, Kwon, Junehee, Todd, Ewen, Perez Rodriguez, Fernando, & Ryu, Dojin. (2016). Adequate Hand Washing and Glove Use Are Necessary To Reduce Cross-Contamination from Hands with High Bacterial Loads. Journal of Food Protection, 79(2), 304–308. https://doi.org/10.4315/0362-028X.JFP-15-342
Sutton, Scott. (2010). The importance of a strong SOP system in the QC microbiology lab. Journal of GXP Compliance, 14(2), 44.
World Health Organization. (2009). Good Laboratory Practice Handbook. Retrieved from https://www.who.int/tdr/publications/documents/glp-handbook.pdf