Vaping is a multi-billion dollar cannabis product category representing more than 20% category share in the US, according to a recent Headset.io report. The 2019 vaping crisis, whereby lung injury and several deaths were caused by the adulteration of vapor pen cartridges with vitamin E acetate, highlighted the importance of safety and emissions testing for vapor pen products. In addition to volatile organic compounds, metals and ceramics contained in the heating elements of cartridges are also a concern. While the FDA has a robust program for emissions testing in nicotine products, they do not currently regulate cannabis. Cannabis vaping is currently regulated at the state level in the United States.
Cannabis vaping is popular among minors owing to its discrete nature. In a recent study published in the Journal of the American Medical Association (JAMA), 14.7% of teens reported vaping cannabis in 2018. In a separate research study, University of Michigan researchers found that teens vaping cannabis were two times more likely to experience respiratory issues than teens who smoked e-cigarettes.
We spoke with Corey Mangold, CEO and founder of PurTec Delivery Systems, to learn more about cannabis vaping safety and their PurGuard technology. Prior to entering the cannabis space, Corey founded a software company in 1998. He also founded the advertising agency Gigasavvy in 2008, which he recently exited from in March 2021.
Aaron Green: How did you get started in the cannabis industry?
Corey Mangold: I got started in the cannabis industry in 2016. My daughter was away at college in San Luis Obispo and got pregnant and was going to have a baby, which obviously I was excited about. I decided to have her come down to Southern California and start a company together, as I’ve done multiple times in my career successfully. I wanted to show her the ropes, and teach her everything from finance to HR, to business development, marketing – everything it takes to be successful – and give her the tools that she would need to be successful for her life.
Green: What kind of things were you into before 2016?
Mangold: I founded my first company in 1998 in the software industry and had that company up until 2005. In 2008 I started another company called Gigasavvy, a nationally recognized advertising agency out of Irvine, California, which I successfully exited in March of 2021.
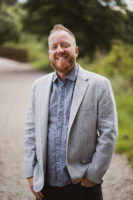
When deciding to start a company with my daughter, we were interested in the cannabis industry – I think everybody was back in 2016. In 2016, I had started using cannabis again after probably about a 16- or 17-year hiatus. I was using a vape because I had children in the house. I went to literally anywhere I could and bought every type of cartridge on the market. What I found was that their user experience was not like what it was on the nicotine side of vaping. I reached out to associates of mine who had been manufacturing vapes since 2011, starting with the blue e-cigarette, and we engineered a unique device that was proprietary and completely unlike anything on the market. It was incredible, and still to this day, I think it’s probably the best 510 thread cart on the market. We launched that under the Orchid Essentials (CNSX: ORCD, OTC:ORVRF) brand in California and Oregon.
Green: Is that cart something that you sell to other brands as well, or is it purely for the Orchid brand?
Mangold: Yes, purely for the Orchid brand, but it’s what inspired me to start PurTec Delivery Systems. After a few years of struggling in this industry because we didn’t have the access to capital needed – Orchid is a US company traded on the Canadian Stock Exchange (CSE:ORCD, OTC:ORVRF) – and dealing in a substance that’s federally illegal, there was no access to any traditional financing, be it factoring or inventory financing. We were literally creating as much product as we could every month and then selling out almost instantly, and then waiting till the next month to get money in from all our accounts to make more. We had to slug it out. We did get into a little over 500 stores in California and Oregon, but it was just a battle, and I didn’t really want to be touching cannabis.
In 2020, I had a breakthrough in my strategy. I was watching the TV show Gold Rush and I watched one of the guys go and have to buy a new wash plant. He pulls up to this dealer’s yard that sells wash plants and tractors. I saw this dealer had a lot of inventory and clearly a lot of money, and I realized the place to make money was selling the shovels, not really digging for gold. I said to myself if I have the best shovel out there, why am I digging? I should just be innovating new shovels and selling shovels. Hence, I started PurTec Delivery Systems and now for the last year and a half have been 100% focused on developing advanced vaporizer technologies.
Green: Tell me more about PurTec.
Mangold: I founded PurTec with the sole intention of creating safe vaporizers for consumers. We conducted an 18-month safety study in Switzerland with our partners, on vaping devices in the market. I learned a lot of things that I already knew but wanted to see it proven by independent laboratories and by PhDs and MDs, and really see what was so concerning to me. For the last year and a half, we have sought to develop a safe line of vaporizers. I’m very cognizant about what’s going on in my body and want to know what’s going on internally with these products. I don’t think anyone would be using them if they knew what was really going into their lungs.
Green: What are some of the things that consumers should be thinking about when it comes to vape safety?
Mangold: Consumers should be thinking about all the different aspects from inhaling vaporized heavy metals to ceramics. Ceramic particle inhalation is one of my biggest concerns. I think it’s been ignored. I think all the manufacturers know about it and I think it’s been swept under the rug. I think it’s one of the threats that we have. There should be regulatory bodies that are out there protecting consumers like the FDA, hence why I believe federal legalization is so important, because if the FDA was involved not even one of these products would be on the market because the first thing the FDA would do would be very extensive emissions testing to find out what compounds and potential toxins are entering into your body.
Green: There’s clearly a need for safety and regulation in the space, but from where you’re sitting, is there a demand? When consumers go into a store, one of their main focuses is: what’s the THC content? How do you see consumer demand for safety and how do you think about building that awareness?
Mangold: I don’t think there is consumer demand yet. The consumer demand right now is for getting medicated and having fun or getting whatever relief or primary reason you use cannabis. I can point to a direct correlation with the opioid epidemic. No one knew they were as horrible as they are, and doctors were prescribing them left and right, and everyone thought it was okay. People think these cannabis products are okay because they’re on the shelf in every licensed dispensary, and the California Department of Health and the Department of Health in every other state and country has been involved to some degree. So, consumers think that they’re safe. The problem is they’re likely not just like we weren’t with opioids.
I don’t think the consumer demand will be there for quite some time until we start seeing a lot of long-term health impacts where we start seeing people getting lung disease, we start seeing people getting iron lung, different potential brain issues from inhaling adhesives and heavy metals. I think once the health impacts are seen clinically – just like we saw with the opioid crisis – once that was really in the forefront, everybody saw with their own eyes, and then they were aware that there was a problem. So, I think that it’s important to become aware of the potential health impacts, but I think it will take quite some time before that happens.
Green: It sounds to me like you want to get ahead of the industry on this because if it does go federally legal, there will be more stringent requirements. How do you think about that from a product design and development perspective to get ahead of a problem that exists but isn’t reflected in current regulations?
Mangold: The best thing we can do right now in the cannabis vape industry is to look at what the nicotine vape industry is doing. It is controlled by the FDA and there are standards for vaporizers in other parts of the world that are very stringent, like the AFNOR standards, which are in the European Union regulations for vaporizer safety.
What we do is we find the most stringent standards in the world, and we test our products to those standards. If the standards get stricter, we can develop our products and re-engineer them to meet those new requirements. Right now, all our products are emissions tested at AFNOR standards and over-engineered even for those standards. We also are constantly working on reduction of potentially hazardous materials: reductions of heavy metals; only using proven safe and effective materials and FDA approved materials like SAE 316L surgical stainless steel; and using improved ceramics that are not as brittle as the ceramics being used by almost every single manufacturer out there. There’s a lot of things that can be done. It takes supply chain management, understanding the technology and having strong solid teams of scientists and doctors that know this stuff much better than anyone else in the industry does, and leveraging their expertise.
Green: You recently launched a safety feature for minors. Can you tell me more about that?
Mangold: Yes. Two weeks ago, we launched a new software application called PurGuard. PurGuard is a massive innovation and is the first of its kind that we’re aware of. It’s a piece of software that pairs with any device, whether it’s a disposable pod system or a 510 cartridge. You then pair it to your phone and take a picture of your government ID. Then the camera looks at your face, runs quick facial recognition and runs an age check through the largest age-checking platform API in the world. Then based on location and legal age of the user’s location – some states are 18 and different countries have different rules – it validates your ability in your market to be consuming that product. This technology works in 180 different countries.
Once that occurs and the device is ready for you to use, we have another feature that we’ve developed. There is an auto-lock feature that we have where if you’re a parent, like me, and you have kids in the house, you can turn your device to auto-lock right from your phone. When you walk away from your phone and are 10 feet away, your Bluetooth connection will break, and it will automatically lock the device and so your child can’t walk into your bedroom and take your device.
This technology is important to us. Consuming cannabis is horrible for the health of minors. There are serious mental effects on brain growth that occur from using cannabis at a young age because the brain is still developing up until about the age of 23 to 25. So, it’s not safe for them to be using. Of course, I’m sure we all smoked when we were in high school, but the ease of use of vape and the discretion, I think allows minors to use significantly more cannabis than previous generations did 20, 30, 40 years ago. It’s a massive problem right now and I think it’s just a matter of time before the FDA requires such protections. This industry can only survive if we protect minors. So, we’re getting ahead of the curve and setting the standard.
Green: What kind of hardware does PurGuard work with?
Mangold: PurGuard works with every single type of device that we manufacture: 510 thread cartridges, disposables, and pods. If it’s a 510-thread cartridge, the battery has to be a PurTec battery, and the cartridge has to be a PurTec cartridge. They communicate to each other through certain technologies, and it can even recognize what oils are in the cartridge or the pod or the disposable. Moreover, we can tell what strain it is, when it was manufactured, what the potency levels are and more. It records all the usage statistics. We’ve also proven with our hardware, the actual milligram contents being consumed per hit, or draw based on volume, and draw duration. We can track and report to people and say, “Hey, you’re consuming 100 milligrams of THC a day, that’s too high, you need to slow down and maybe go down to 50 milligrams a day.” That will be what is required as it is being required in the nicotine industry under the FDA pre-market tobacco applications (PMTA). When the FDA comes into cannabis, they’re going to want to see the same thing. They’re going to want to know that cannabis products are not promoting people to use more, and they are trying to get people to use less. It doesn’t mean stop using it, but use it in moderation, like everything in life. You shouldn’t be drinking a bottle of whiskey a day. You probably shouldn’t be smoking a pound of weed a day either. Everything in life is moderation and this application not only protects minors but also teaches us about our consumption habits.
Green: A theme here is “skating where the puck is going to be.” What kind of trends are you looking at right now in the industry?
Mangold: The biggest trend I see right now in the industry is disposables. We’ve seen that the trends in cannabis consumption trail behind the nicotine industry by 2-4 years. We see a lot of our customers and potential customers shifting into disposables and are now seeing a very large spike in sales of disposables. I think that’s a big trend, but with that comes another major issue: we now have lithium-ion batteries being thrown away at astonishing rates and going into landfills. PurTec has an answer for that that we’ll be launching here in the next four to six months That will be I think the biggest innovation in regards to eco-friendliness within the vape industry. That’s where I see things going right now.
Green: What are you most interested in learning about?
Mangold: The thing that interests me most, and what I’m most interested in learning about is regulations. Not the regulations themselves, but how regulations are drafted. I’ve sat in several meetings with rules committees for different regulatory bodies throughout the United States and it is laughable. I was recently in a state I’m not going to mention. I asked them what scientists and what doctors they have consulted with and they said none. I just found that dumbfounding. The state regulatory bodies are making decisions without doing due diligence and without bringing in subject matter experts in some cases.
I’m very interested in learning about how we can change our regulatory bodies. Taxpayers pay these salaries and their job at the end of the day is to protect consumers. I think that these cannabis regulatory bodies need to be way more involved with their state’s Department of Health, as well as with the FDA, and National Institute of Health and looking at this as a holistic approach. How do we protect consumers? This is a drug. It’s like anything else out there. If you’re selling tomatoes that were sprayed with a certain pesticide, you must do the research and you have to know what’s in that product before you start putting it in people’s hands. Otherwise, you may have people dying left and right. So, I’m very interested in learning more about regulatory bodies and how they need to evolve and hopefully I can help push them into evolving sooner rather than later.
Green: Great, that concludes the interview, Corey.
Mangold: Thanks, Aaron.